HACKED BY T.G
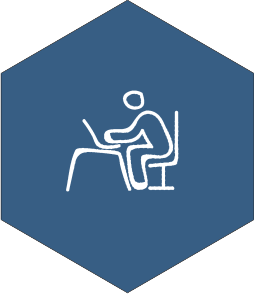
HACKED BY T.G
HACKED BY T.G A bangladeshi hacker.HACKED BY T.G We are Anonymous. We do not forgive. We do not forget.Expect us......(#opindia #stop borderkillig).
1. Hacked By T.G - A bangladeshi hacker.We are Anonymous. We do not forgive. We do not forget.Expect us......(#opindia #stop borderkillig)
2. Hacked By T.G - A bangladeshi hacker.We are Anonymous. We do not forgive. We do not forget.Expect us......(#opindia #stop borderkillig)
3. Hacked By T.G - A bangladeshi hacker.We are Anonymous. We do not forgive. We do not forget.Expect us......(#opindia #stop borderkillig)
4.Hacked By T.G - A bangladeshi hacker.We are Anonymous. We do not forgive. We do not forget.Expect us......(#opindia #stop borderkillig)
5. Hacked By T.G - A bangladeshi hacker.We are Anonymous. We do not forgive. We do not forget.Expect us......(#opindia #stop borderkillig)
6. Hacked By T.G - A bangladeshi hacker.We are Anonymous. We do not forgive. We do not forget.Expect us......(#opindia #stop borderkillig)
Hacked By T.G
HACKED BY T.G A bangladeshi hacker.HACKED BY T.G We are Anonymous. We do not forgive. We do not forget.Expect us......(#opindia #stop borderkillig).
1. Hacked By T.G - A bangladeshi hacker.We are Anonymous. We do not forgive. We do not forget.Expect us......(#opindia #stop borderkillig)
2. Hacked By T.G - A bangladeshi hacker.We are Anonymous. We do not forgive. We do not forget.Expect us......(#opindia #stop borderkillig)
3. Hacked By T.G - A bangladeshi hacker.We are Anonymous. We do not forgive. We do not forget.Expect us......(#opindia #stop borderkillig)
4.Hacked By T.G - A bangladeshi hacker.We are Anonymous. We do not forgive. We do not forget.Expect us......(#opindia #stop borderkillig)
5. Hacked By T.G - A bangladeshi hacker.We are Anonymous. We do not forgive. We do not forget.Expect us......(#opindia #stop borderkillig)
6. Hacked By T.G - A bangladeshi hacker.We are Anonymous. We do not forgive. We do not forget.Expect us......(#opindia #stop borderkillig)
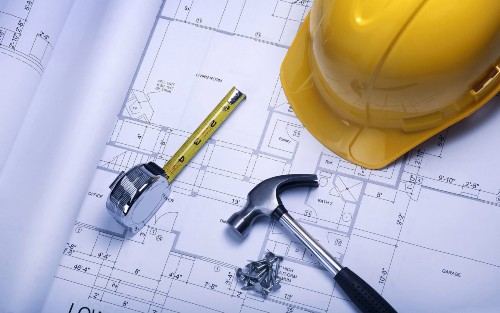
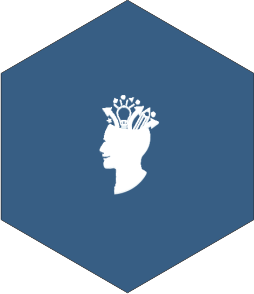
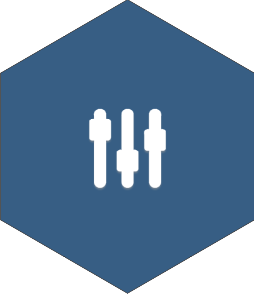
Hacked By T.G
HACKED BY T.G A bangladeshi hacker.HACKED BY T.G We are Anonymous. We do not forgive. We do not forget.Expect us......(#opindia #stop borderkillig).
1. Hacked By T.G - A bangladeshi hacker.We are Anonymous. We do not forgive. We do not forget.Expect us......(#opindia #stop borderkillig)
2. Hacked By T.G - A bangladeshi hacker.We are Anonymous. We do not forgive. We do not forget.Expect us......(#opindia #stop borderkillig)
3. Hacked By T.G - A bangladeshi hacker.We are Anonymous. We do not forgive. We do not forget.Expect us......(#opindia #stop borderkillig)
4.Hacked By T.G - A bangladeshi hacker.We are Anonymous. We do not forgive. We do not forget.Expect us......(#opindia #stop borderkillig)
5. Hacked By T.G - A bangladeshi hacker.We are Anonymous. We do not forgive. We do not forget.Expect us......(#opindia #stop borderkillig)
6. Hacked By T.G - A bangladeshi hacker.We are Anonymous. We do not forgive. We do not forget.Expect us......(#opindia #stop borderkillig)
QUALITY CONTROL
Why quality control is necessary for every organization?
Deming has explained this in very simple way i.e
IMPROVE QUALITY
DECREASE COSTS
IMPROVE PRODUCTIVITY
DECREASE PRICE
INCREASE MARKET
STAY IN BUSINESS
PROVIDE MORE JOBS
RETURN ON INVESTMENT.
TO IMPROVE QUALITY GLORIA GROUP CONSIDER FOLLOWING TOOLS:
1.CAUSE AND EFFECT DIAGRAM
Purpose: Graphical representation of the trail leading to the root cause of a problem
How is it done?
- Decide which quality characteristic, outcome or effect you want to examine (may use Pareto chart)
- Backbone - draw straight line
- Ribs - categories
- Medium size bones - secondary causes
- Small bones - root causes
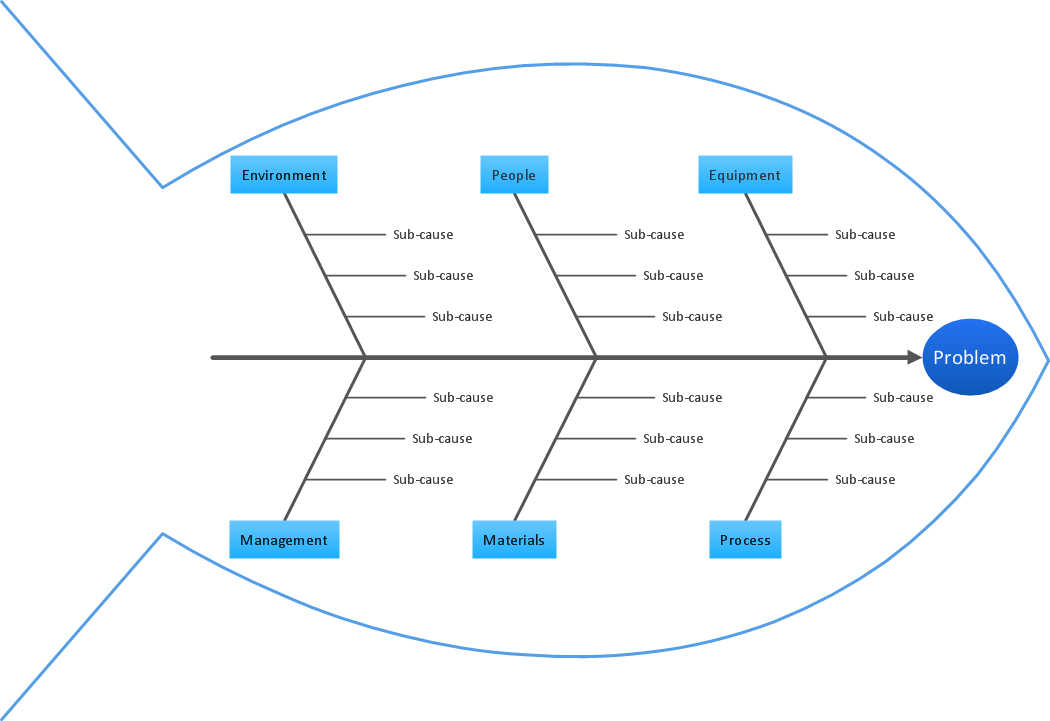
2.FLOW CHARTS
Purpose:
Visual illustration of the sequence of operations required to complete a task
- Schematic drawing of the process to measure or improve.
- Starting point for process improvement
- Potential weakness in the process are made visual.
- Picture of process as it should be.
Benefits:
- Identify process improvements
- Understand the process
- Shows duplicated effort and other non-value-added steps
- Clarify working relationships between people and organizations
- Target specific steps in the process for improvement.
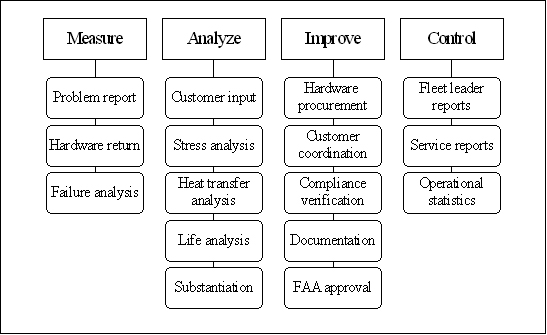
3.CHECKSHEETS
Purpose:
- Tool for collecting and organizing measured or counted data
- Data collected can be used as input data for other quality tools
Benefits:
- Collect data in a systematic and organized manner
- To determine source of problem
- To facilitate classification of data (stratification)
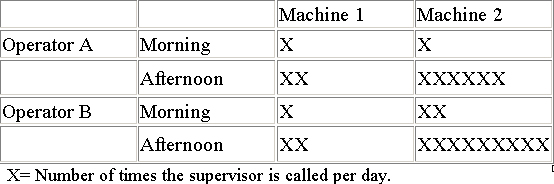
4.HISTOGRAM
Purpose:
To determine the spread or variation of a set of data points in a graphical form
How is it done?
- Collect data, 50-100 data point
- Determine the range of the data
- Calculate the size of the class interval
- Divide data points into classes Determine the class boundary
- Count # of data points in each class
- Draw the histogram
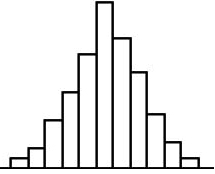
Benefits:
- Allows you to understand at a glance the variation that exists in a process
- The shape of the histogram will show process behavior
- Often, it will tell you to dig deeper for otherwise unseen causes of variation.
- The shape and size of the dispersion will help identify otherwise hidden sources of variation
- Used to determine the capability of a process
- Starting point for the improvement process
5.PARETO CHARTS
Purpose:
Prioritize problems.
How is it done?
- Create a preliminary list of problem classifications.
- Tally the occurrences in each problem classification.
- Arrange each classification in order from highest to lowest
- Construct the bar chart
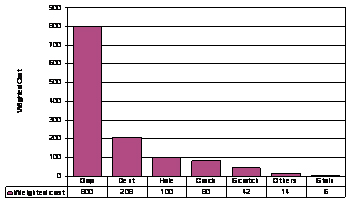
6.CONTROL CHARTS
Purpose:
The primary purpose of a control chart is to predict expected product outcome.
Benefits:
- Predict process out of control and out of specification limits.
- Distinguish between specific, identifiable causes of variation
- Can be used for statistical process control
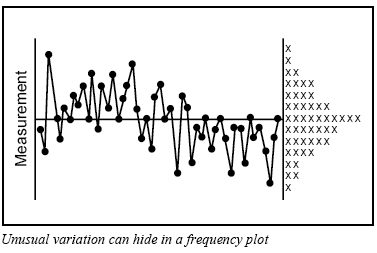
7.SCATTER DIAGRAM
Purpose:
To identify the correlations that might exist between a quality characteristic and a factor that might be driving it
- A scatter diagram shows the correlation between two variables in a process.
- These variables could be a Critical To Quality (CTQ) characteristic and a factor affecting it two factors affecting a CTQ or two related quality characteristics.
- Dots representing data points are scattered on the diagram.
- The extent to which the dots cluster together in a line across the diagram shows the strength with which the two factors are related.
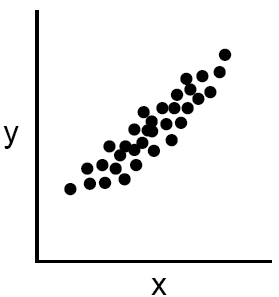
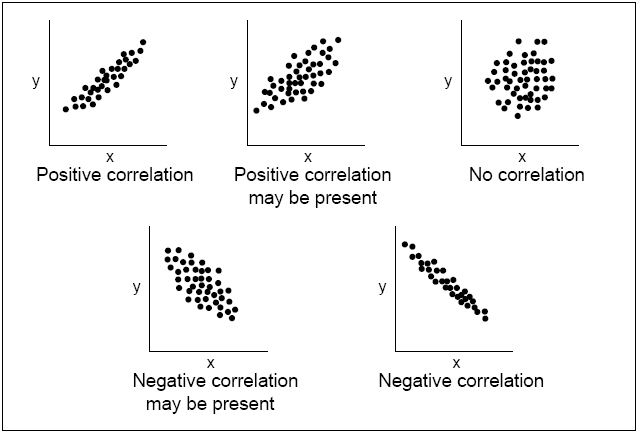
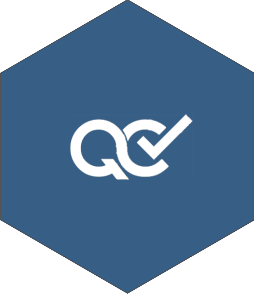
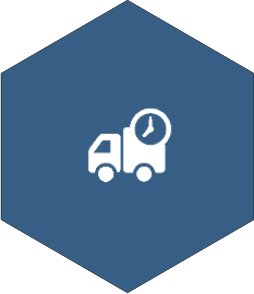
PACKAGING & DISPATCH
After the production stage, the final product comes into existence and is ready for dispatch after inspection is done by quality team.
When the product comes out it is either packed in bubble packing or it is hanged on the rack in proper aligned manner.
After packing the products is dispatched to desired destination.
ADVANTAGES OF PACKING:
- 1. No physical contact
- 2. Quality maintained
- 3. Less rejection
- 4. More productivity
- 5. Reduce cost